
The Reliable Sealing Solution for Your Industry
Spiral wound gaskets are metal-based gaskets designed for flanges, valves, and critical sealing needs. They feature helically wound metal strips shaped like a V or W. Combined with flexible filler material, they create a strong seal. The metal provides strength and pressure resistance. Meanwhile, the filler prevents leaks and ensures tight sealing. This design allows spiral wound gaskets to handle extreme conditions effectively.
Advantages of Spiral Wound Gaskets
Spiral wound gaskets bring multiple advantages to various applications:
Extreme Temperature Resistance: Suitable for harsh environments with high temperatures.
Perfect Seal: The metal and filler combination prevents fluid leakage.
High Flexibility: Available in various types and sizes for different needs.
Superior Durability: Built from high-quality materials for long-term use.
Easy Installation: Quick to install and remove, reducing downtime.
These benefits make them highly valued in critical industries.
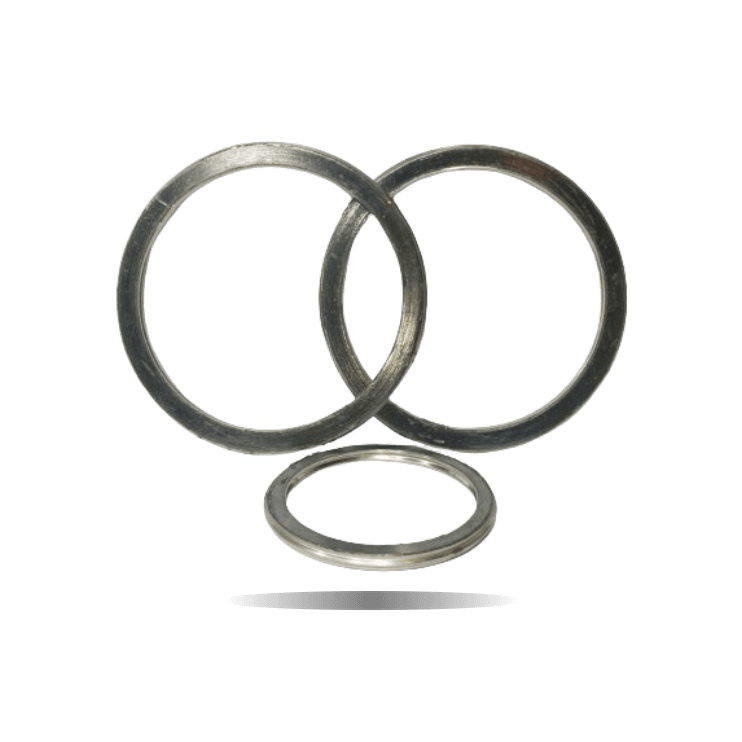
B Style
Style B gasket consists of sealing element only. It comes with some additional layers of winding strip when used in tongue and groove and male/female flanges. It is available in various shapes, including oval, obround, and diamond.
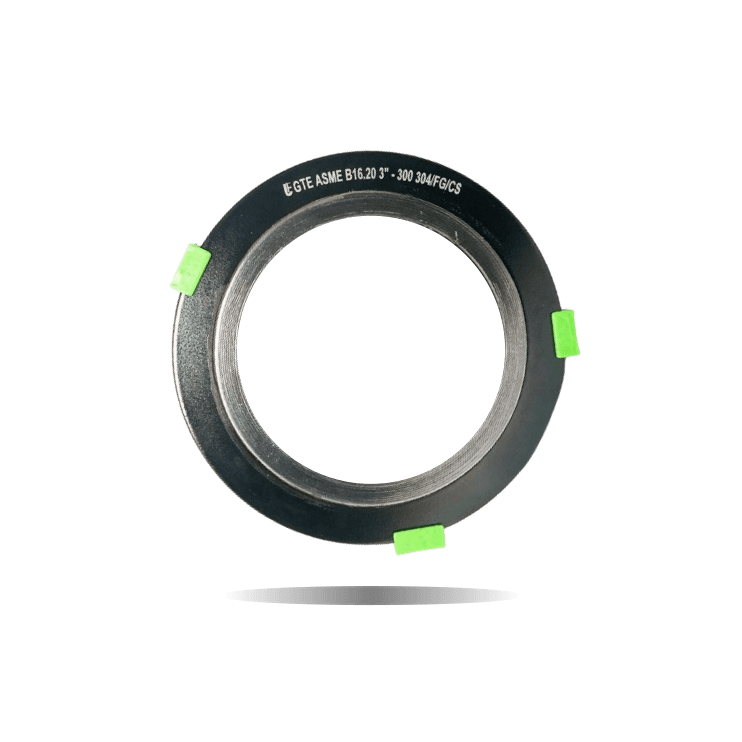
OB Style
This type of gasket consists of outer ring and sealing element. It is most suitable for RF and FF flanges. We made it accordingly standards to guarantee its quality.
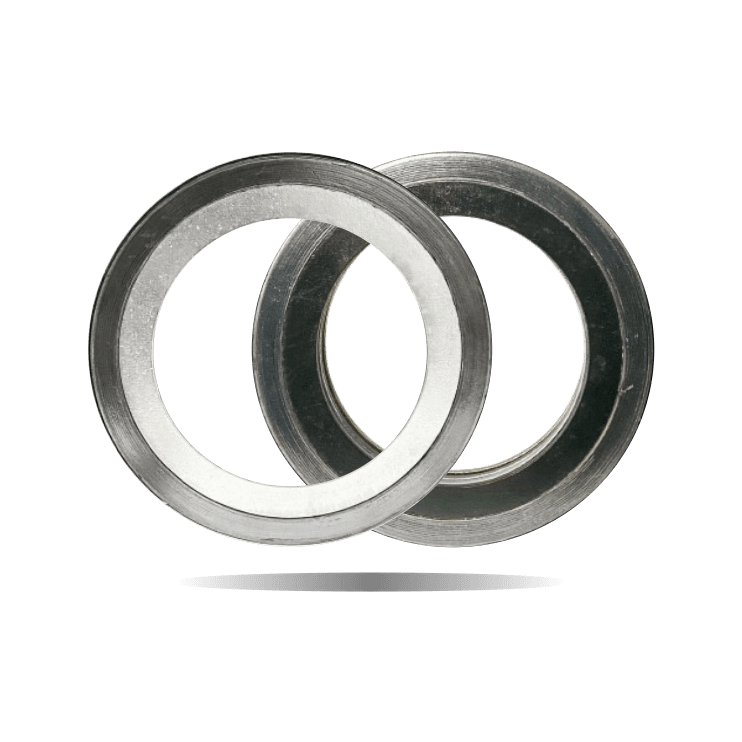
BI Style
The standard BI style consists of an inner ring and a sealing element. This ring is heat and corrosion resistant. This ring is also available in various shapes such as oval, obround, diamond, etc.
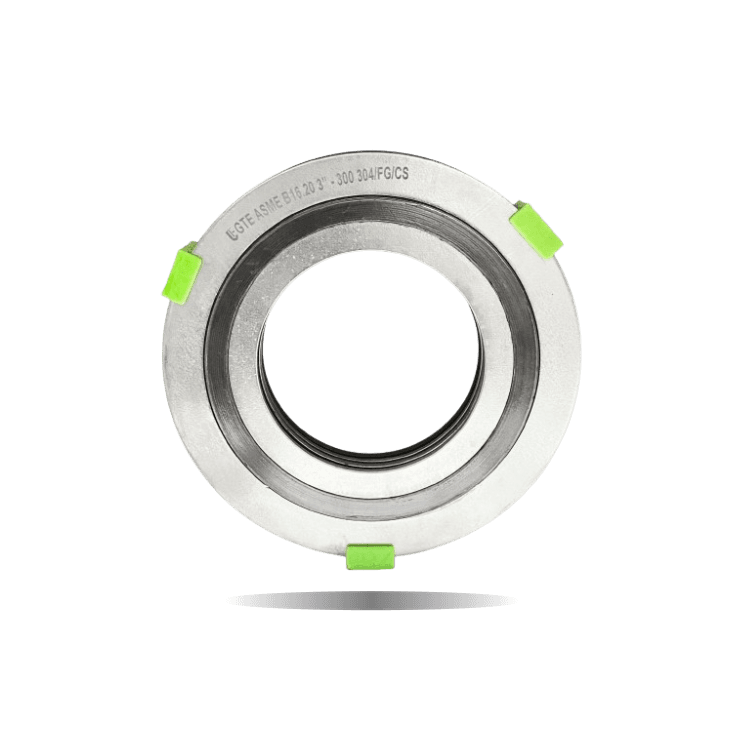
OBI Style
The standard OBI style consists of outer ring, sealing element, and inner ring. The outer ring is color coded based on the material that constructs it. It is heat and corrosion resistant due to its extra inner ring fitted that provides an additional compressions stop.

Spiral wound gaskets consist of three key parts :
- Materials:*
- Stainless Steel: The most common choice due to its corrosion resistance and extreme temperatures. Commonly used types include SS304, SS316, and SS316L.
- Description: The metal winding forms the main structure of the gasket, providing mechanical strength and pressure resistance. The winding shape is usually V or W, which clamp the filler material.
- Materials:*
- Materials:*
- Graphite: Resistant to high temperatures and has good compression capabilities, suitable for applications with extreme temperatures and pressure fluctuations.
- PTFE (Polytetrafluoroethylene) : Chemically resistant and has a low coefficient of friction, ideal for applications with corrosive fluids.
- Ceramic Fiber: Withstands very high temperatures and has good thermal insulation properties.
- MICA : is a group of silicate minerals that have a layered structure and Some common types of mica are muscovite and phlogopite. Mica has good heat resistance, high electrical insulation, and is chemically stable.
- Other Non-Asbestos Materials : Other materials can also be used as filler materials, depending on the application and working conditions.
- Description: The filler material acts as the primary seal, filling small gaps on the flange surface and preventing leakage. The filler material should be selected according to the type of fluid, temperature, and working pressure.
- Materials:*
- Materials:*
- Carbon Steel: used for the inner ring or outer ring due to its strength and economical price.
- Stainless Steel: Used for the inner ring or outer ring if better corrosion resistance is required.
- Description: The ring serves to provide additional stability to the gasket and protect the winding from damage. The outer ring also helps center the gasket when installed on the flange.
- Materials:*
Together, these components create a durable and flexible sealing system.
Selecting the correct gasket material is crucial for performance. Consider these factors:
Type of fluid sealed.
Operating temperature range.
Working pressure conditions.
Environmental exposure risks.
Proper material choice ensures reliable sealing and longer gasket life.
Our spiral wound gaskets use only top-grade materials:
Metal Winding: Stainless steel (SS304, SS316, SS316L).
Filler Material: Graphite, PTFE, ceramic, or MICA.
Rings: Carbon steel or stainless steel for added durability.
These materials ensure maximum performance in demanding applications.
Â
Application For Industries
Oil and Gas Industry :
In the oil and gas industry, spiral wound gaskets are used in various equipment such as:
- Pipes and Flanges : Sealing pipe and flange connections to prevent leaks of oil, gas, or drilling fluids.
- Valves : Used in valves to ensure tight closure and prevent fluid leakage.
- Pumps : Sealing pump components to prevent leaks and maintain efficiency.
- Heat Exchangers : Used in heat exchangers to prevent leaks of coolant or processed fluids.
Petrochemical Industry :
Spiral wound gaskets are also widely used in the petrochemical industry, particularly in :
- Reactors : Sealing reactors to prevent leaks of hazardous chemicals.
- Storage Tanks : Used in storage tanks to prevent leaks of chemicals or petrochemical products.
- Piping Systems : Sealing pipe joints in piping systems to prevent chemical leaks.
Chemical Industry :
In the chemical industry, spiral wound gaskets play an important role in :
- Chemical Processing Equipment : Sealing various chemical processing equipment such as reactors, mixers, and tanks.
- Laboratory Equipment : Used in laboratory equipment to ensure tight seals and prevent contamination.
Power Generation Industry :
Spiral wound gaskets are used in the power plant industry for :
- Boilers : Sealing boiler components to prevent leaks of steam or water.
- Turbines : Used in turbines to ensure tight seals and prevent steam leaks.
- Generators : Sealing generator components to prevent coolant leaks.
Food and Beverage Industry :
In the food and beverage industry, spiral wound gaskets are used in :
- Food Processing Equipment : Sealing food processing equipment to ensure hygiene and prevent contamination.
- Packaging Equipment : Used in packaging equipment to ensure tight seals and maintain product quality.
Other Industries :
In addition to the above industries, spiral wound gaskets are also used in various other industries such as :
- Pharmaceutical : In drug production and packaging equipment.
- Water Treatment : In water treatment systems to prevent leaks.
- Pulp and Paper : In paper and pulp production equipment.
Spiral wound gaskets deliver high sealing performance and durability. They resist extreme temperatures and pressures while sealing various fluids.
Their flexibility and strength make them a top choice for industrial sectors worldwide.
We are an experienced provider of spiral wound gaskets for various industries. Our products meet strict quality standards and are available in many sizes and types.
We guarantee reliable sealing solutions tailored to your unique needs.
Need spiral wound gaskets? Contact our expert team for advice or orders. We’re ready to help you find the right solution.
We hope this guide gives valuable insights. Feel free to reach out if you have more questions.